High Efficiency, High Precision,High Torque, Low Noise, Small Backlash
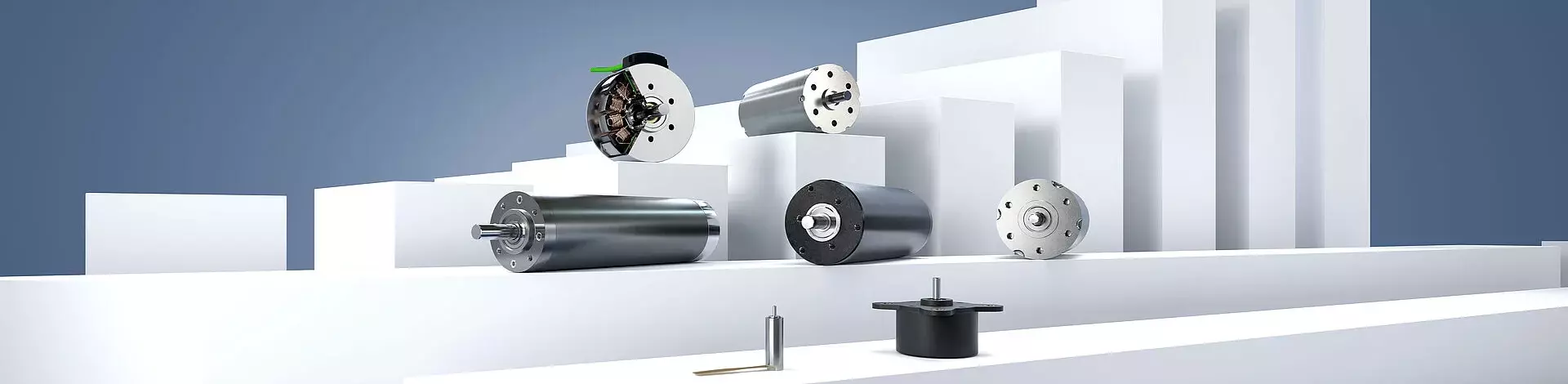
Motor Multi-Dimensional Filtering
Products
DC Planetary Gear motor
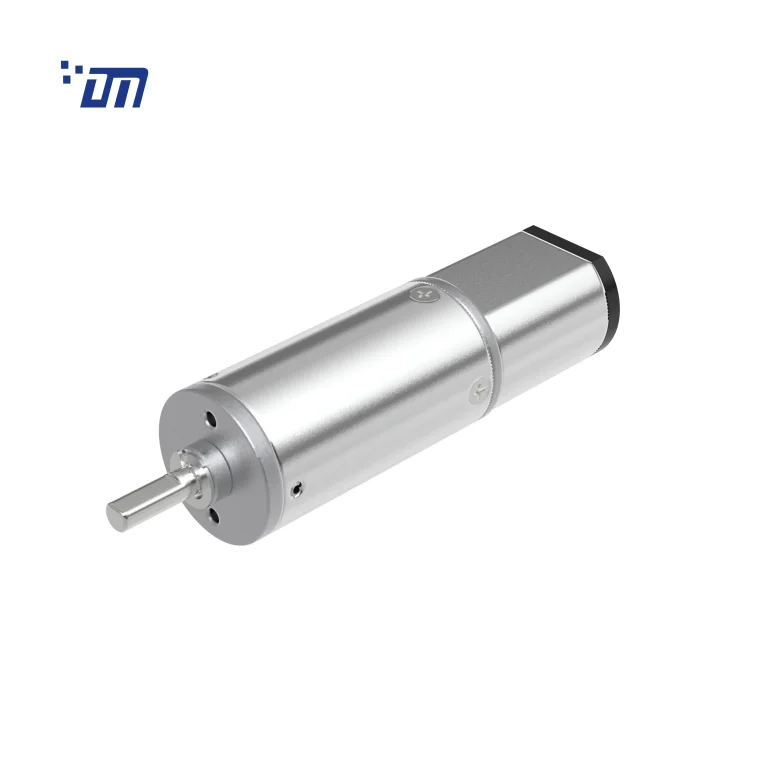
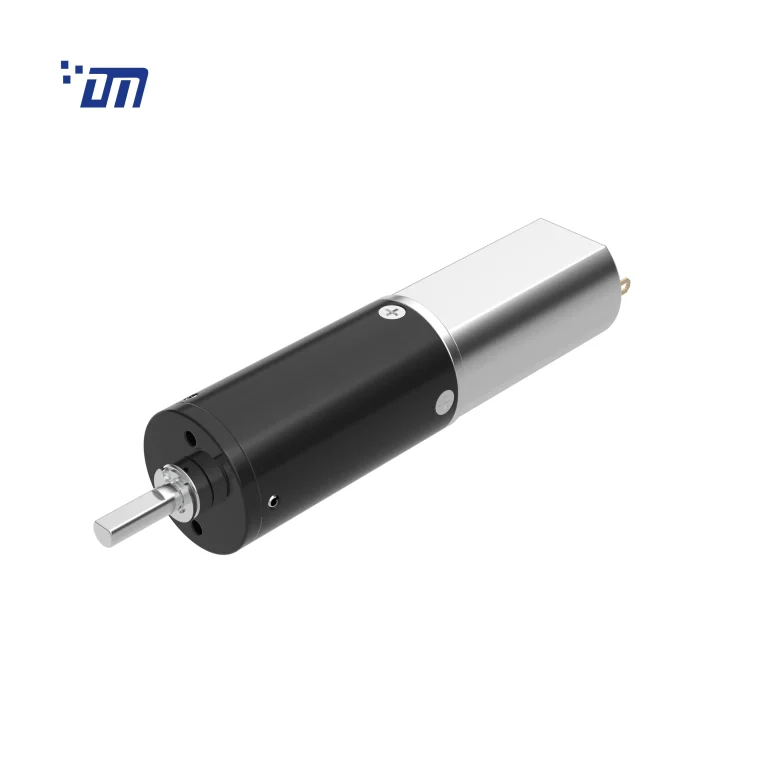
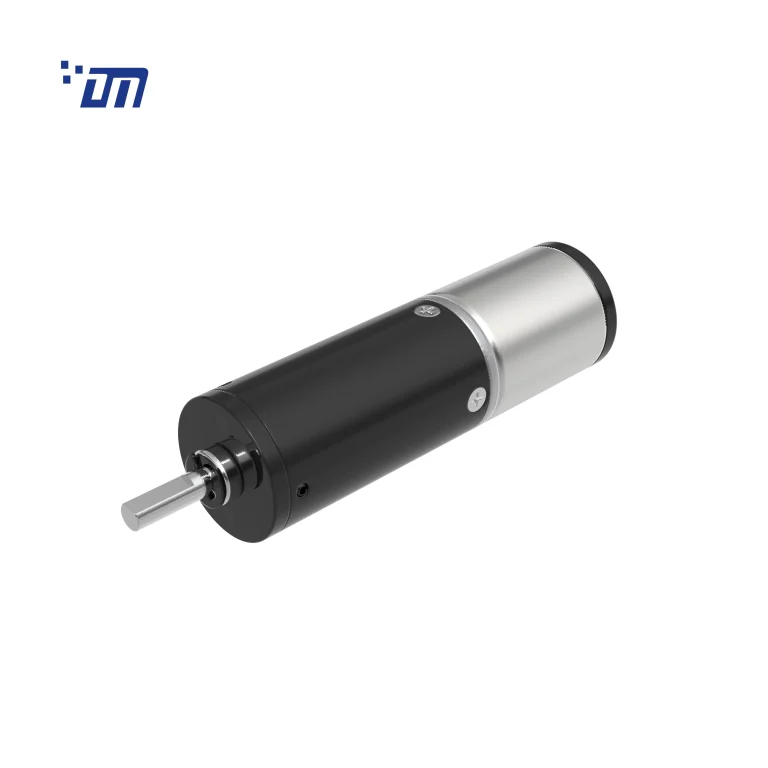
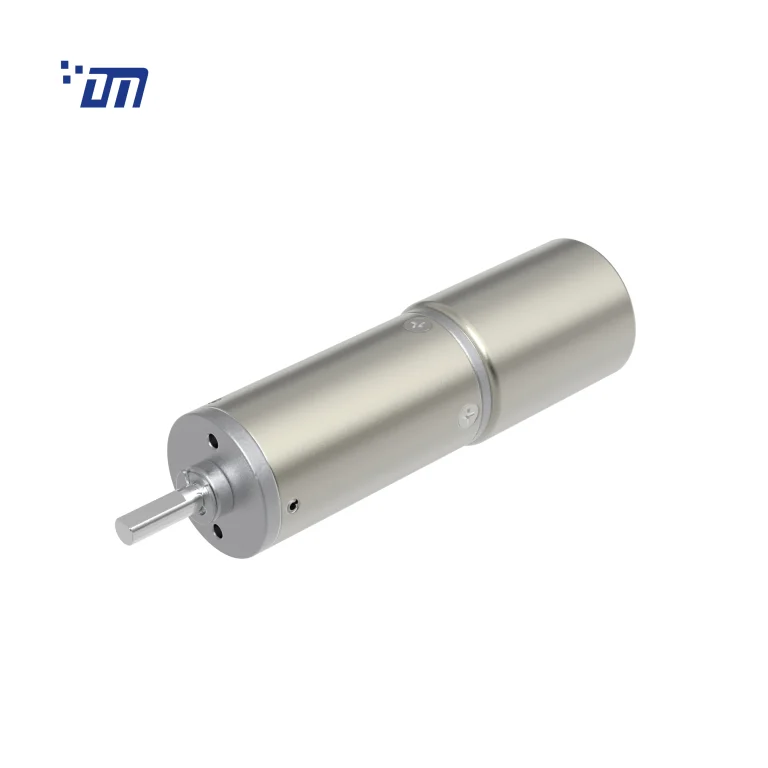
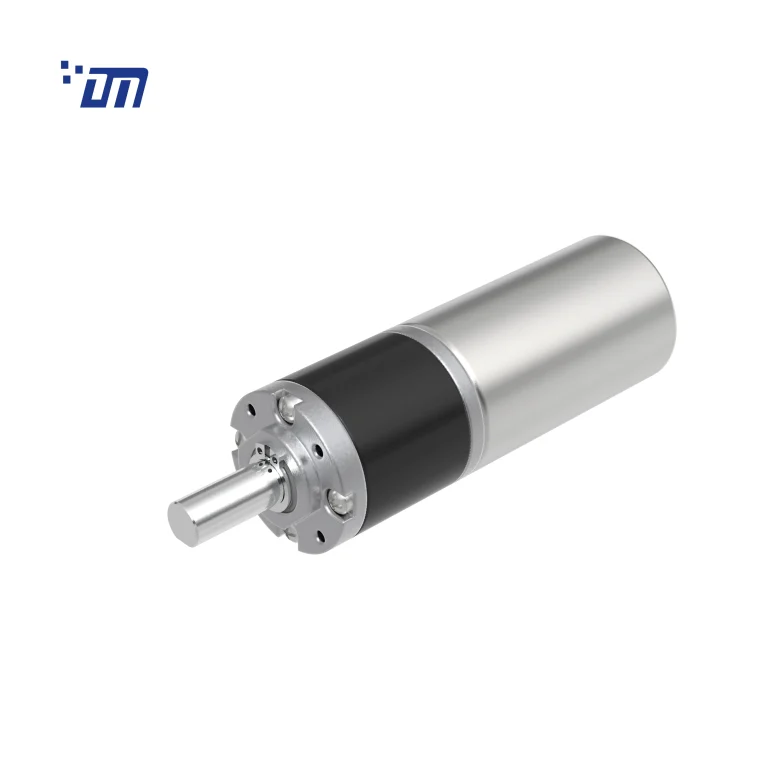
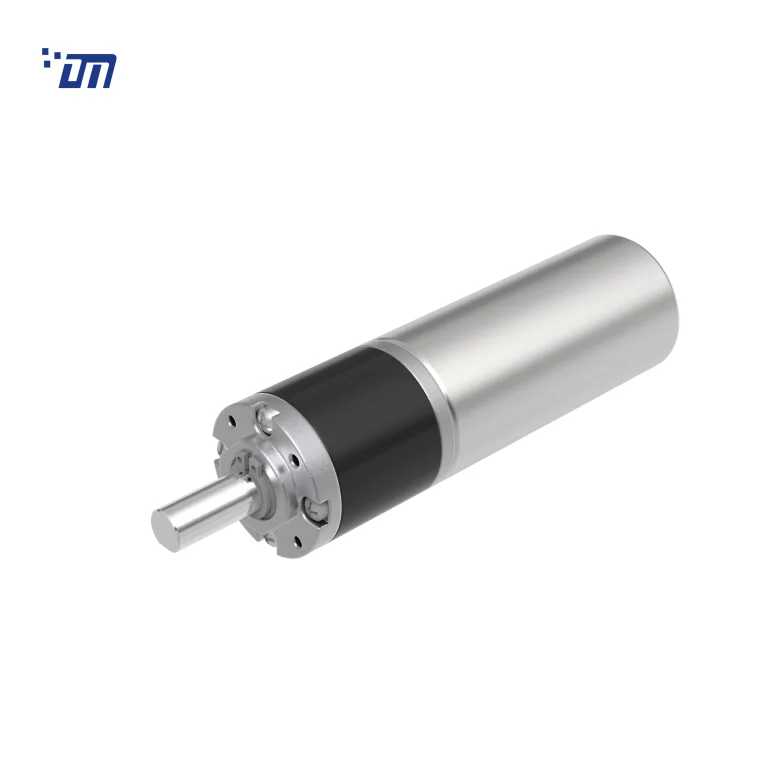
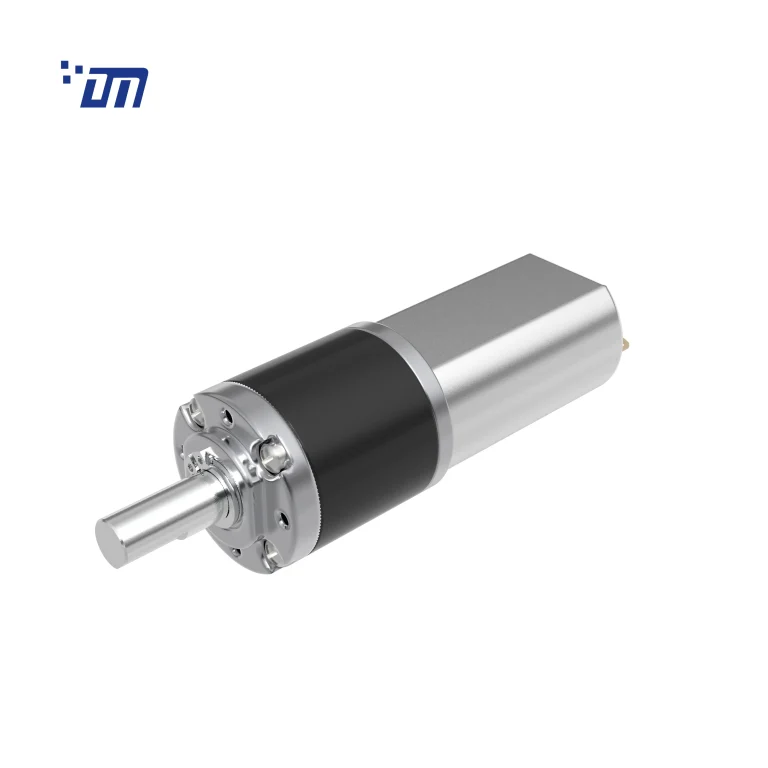
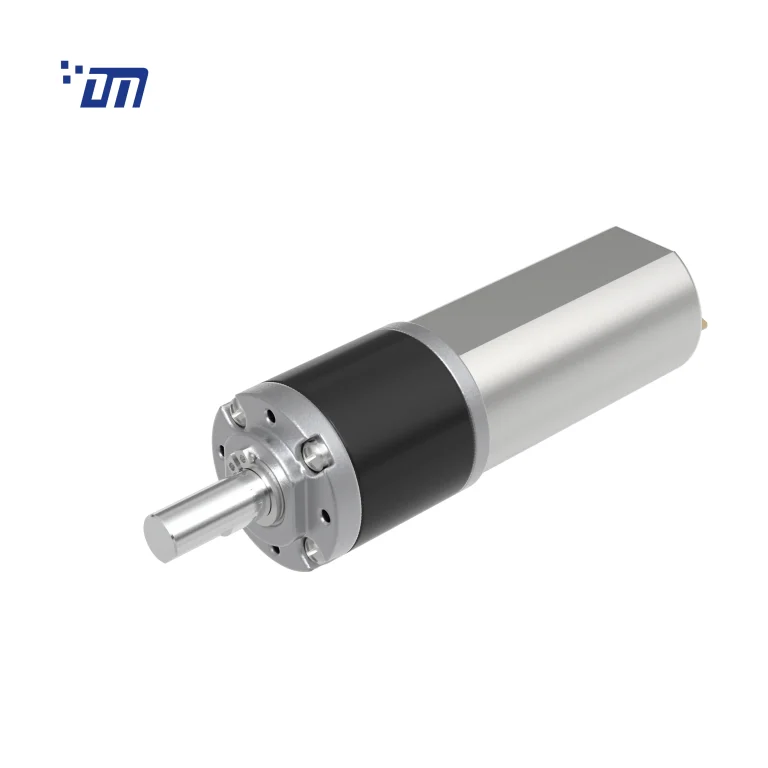
DC Planetary Gear motor
DC Planetary Gear motor is a DC motor with Planetary gearbox. DONGMING Provide Precise Planetary Gear Motor with Low Noise Long Lifespan, High Torque, High Efficiency, High Quality. Offered in Standard or Customized Solutions for Planetary Gear Motor.
The gears inside of a planetary gear head have a unique method of meshing together. They have an internal gear, called the sun gear. The sun gear drives multiple outer gears known as planetary gears. The planetary gears mesh with an outer ring to guide and hold them in place. The outer ring is fixed and incorporated in the motor housing.
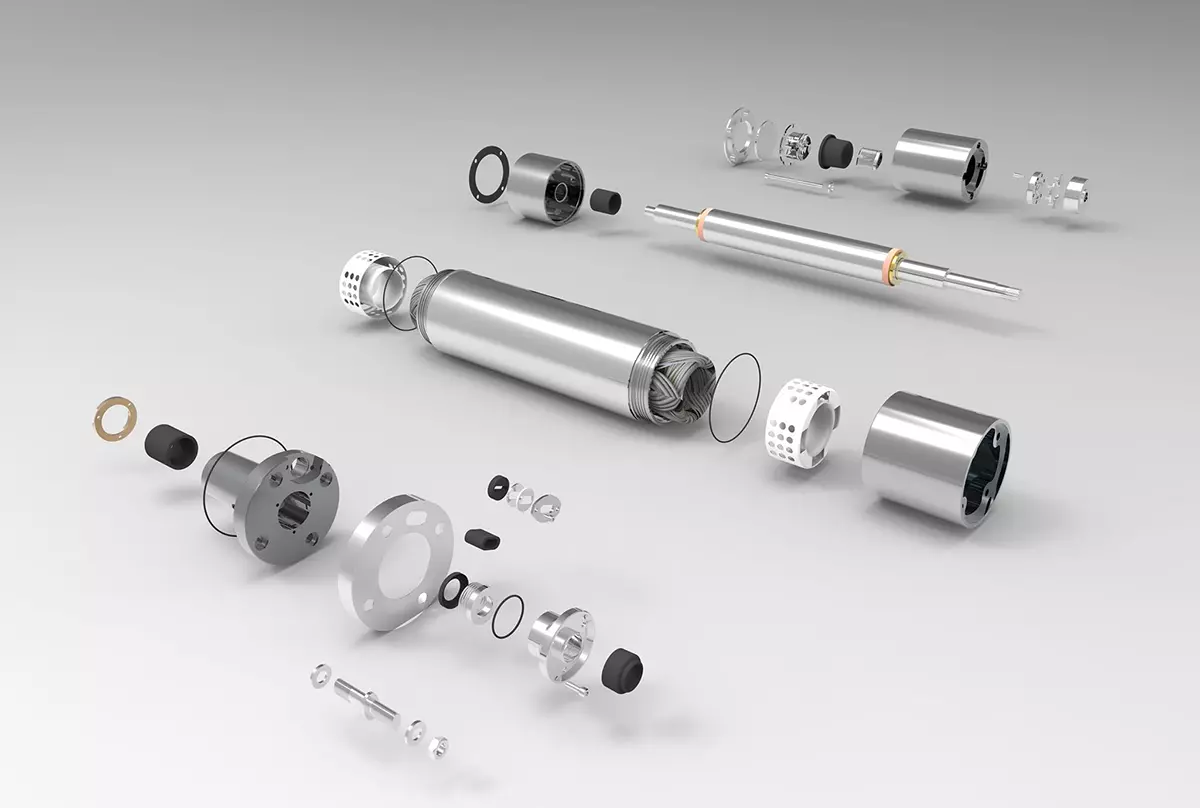
Our Advantages of DC Planetary Gear motor
How to Improve the DC Gear Motor
How to improve the lifespan of gear motor
1. Resonable design and use
In the early stage of design and selection, the output torque of the gearbox should be accurately accounted for to avoid overloading, in order to reduce the fatigue stress and wear of the gears.Select suitable gearbox construction, e.g: planetary construction, to increase the overall strength of the gearbox at the same size
Reasonable design of transmission ratios and load distribution, adjusted according to actual needs, in order to optimize the working condition of gearboxes
Optimize the design, such as selecting a larger modulus and a suitable coefficient of variation, can increase the thickness of the gear teeth, improve the bending strength of the gear and the contact strength of the tooth surface
2. Correctly select gear material and heat treatment process
According to the working environment and load characteristics of the gearbox, selectin high-strength, high wear-resistant gear material is the basis. For example, alloy steel 20CrMnTi and other materials can improve the gear’s load carrying capacity and wear resistance, thus extending the service life of the gearbox.Gear strengthening treatment, such as carburization, carbonitriding heat treatment, can form a layer of high hardness shell on the gear surface, to ensure its stability in a long time when working under high load.
3. Maintain good lubrication
Adequate lubrication is the key to the normal operation of the gearbox, according to the actual working environment of the product (such as temperature, humidity), load, select the appropriate lubricating grease, reduce wear of gears and increase life.How to reduce noise of DC gear motor
1. Reasonably select the gearbox
According to the actual need to choose suitable models, specifications and quality and reliable gear motor, such as spur, planetary or worm structure gearbox, and consider its working environment, such as temperature, humidity, vibration and other factors, in order to avoid the noise caused by environmental factors
Select gearmotor models specifically designed for noise reduction, often with precision gearing and optimized gear geometries2. Improved transmission structure and design
Improve the transmission structure by adjusting the gear mesh clearance, increasing the number of gear teeth, adjusting the gear tooth shape, etc., to reduce the noise.
Helical gears are used instead of spur gears because helical gears have a larger contact area when meshing, which reduces noise. Noise can also be reduced by using appropriate gear trimming techniques
Optimize gear parameters such as shifting parameters, tooth height parameters, pressure angle, center distance, etc. to minimize the meshing-in impact speed and control the ratio of meshing-in impact speed to meshing-out impact speed within a certain range3. Use plastic gear
Under the condition of achieving the torque, replace the metal gear with plastic gear. You can either use ordinary plastic gear or plastic gear made of special materials. Plastic gear made of special materials are not only quieter, but also have a longer life.4. Select brushless motors instead of brushed motors
- Longer Lifespan:
Brushless motors have a long lifespan, thanks in large part to their lack of brushes and commutators, which reduces mechanical wear and the heat generated by friction. In contrast, brushed motors typically have a continuous operating life of a few hundred to more than a thousand hours, after which the carbon brushes need to be replaced or the bearings will tend to wear out and damage the motor. - Higher efficiency and output power:
Since brushless motors are electronically commutated, the contact resistance of the brushes and commutator is reduced, thus lowering the overall resistance and heat generation of the motor. This makes brushless motors more efficient and produces more power. Brushed motors, on the other hand, are less efficient because the current does work on the internal resistance of the motor, resulting in a large degree of conversion of electrical energy into heat1. - Lower Noise:
Brushless motors operate with a corresponding reduction in noise due to reduced frictional resistance. This is a significant advantage for application scenarios that require a quiet environment. - Greater controllability and speed range
Brushless motor adopts digital frequency control, which is more controllable and can realize a wide range of speed regulation from a few revolutions per minute to tens of thousands of revolutions per minute or even more than 100,000 revolutions per minute. Brush motor speed is relatively constant after starting, speed regulation is not so easy. - Reduced interference with radio equipment
Brushless motors do not have brushes and therefore do not generate friction sparks, thus greatly reducing the interference of electrical sparks with radio equipment. This is an important advantage for electronic devices that require high precision and reliability.
In summary, brushless motors show significant advantages in terms of service life, efficiency, noise control, controllability and electromagnetic interference, and are therefore increasingly being used to replace brushed motors.
5. Select the high-quality materials and accessories
Choose low-noise accessories, such as low-noise bearings, low-noise gears, etc. These low-noise accessories can effectively reduce the noise of the geared motor.
Use gear materials with good wear resistance and toughness, such as alloy steel, aerospace plastic, etc. to reduce gear noise during operation.6. Improved precision in manufacturing and installation
Ensure gears are machined with precision and reduce gear backlash to minimize the sound of impact when gears are meshing
Pay attention to the installation of the gearmotor, follow the installation instructions provided by the manufacturer to ensure that the gearmotor and the drive system are closely and stably coordinated to avoid resonance phenomenon.7. Proper lubrication and maintenance
The use of suitable lubricants and lubrication methods to maintain good lubrication of gears, reducing friction and wear, thereby reducing noise8. Additional noise reduction measures
Installation of vibration-damping devices, such as vibration-damping pads or vibration-damping brackets, between the geared motor and the equipment can absorb and reduce the transmission of vibration and reduce noise.
Installation of sound insulation materials around the gear motor to effectively absorb and reduce transmission noise conduction.- Longer Lifespan:
How to strengthen the gearbox
1. Choosing the right material
The first and foremost way to improve the strength of the gear box is to choose high-strength, high-stiffness materials. For example, aluminum alloy, cast iron and other materials because of its good mechanical properties and wear resistance, can effectively resist the external vibration and impact force, reduce the deformation of the box, thereby improving the overall strength and reliability of the gear box work2. Optimized structural design
Adding reinforcement: Adding reinforcement on the inside or outside of the gear box can significantly enhance the structural strength of the box. Reinforcement bars can be made of angle steel, square steel and other metal materials, and through welding or bolt connection with the main structure of the box is closely connected, so that the gear box is not easy to deform when working.Optimizing the shape of the case: designs such as adopting a quadrilateral structure and increasing the thickness of the case and gear chamber can also effectively improve the rigidity and strength of the case. In addition, the use of multi-stage cooling or hot punching process during the processing of the case can further enhance the robustness and durability of the case
3. Improved durability and strength of gears
Precision forging technology: The use of precision forging technology can reduce the deformation of the gear tooth profile during heat treatment, improve the wear resistance of the teeth and the stability of the gear meshing, thereby indirectly enhancing the overall strength of the gearboxOptimized design: By choosing a larger modulus and a suitable variation coefficient, the tooth thickness of the gear teeth can be increased to improve the bending strength of the gear and the tooth contact strength. At the same time, increasing the radius of the tooth root arc also helps to improve the bending fatigue strength of the tooth root.
Material selection: Selection of high-strength gear materials, such as carbon and nitrogen co-infiltration materials (20CrMnTi, etc.), can significantly improve the wear resistance and anti-fatigue properties of the gear, and thus enhance the overall strength of the gearbox.
4. Improved precision in manufacturing and installation
Strict control of machining errors: including tooth shape error, tooth pitch error, tooth direction error, etc. High-precision machining can ensure the accuracy and stability of gear meshing, and reduce the strength reduction caused by manufacturing errors.Ensure installation accuracy: In the assembly process, ensure the parallelism and coaxiality of the gear shaft and the accuracy of the center distance, so that the gears can mesh well and avoid partial load and local wear, thus improving the overall strength of the gearbox.
5. Enhanced lubrication and heat dissipation
Good lubrication and heat dissipation conditions are essential to maintain the high strength of the gearbox. Suitable lubricants should be selected and the lubrication should be optimized according to the conditions of transmission speed, load and working temperature. At the same time, improve the heat dissipation conditions of the gear box, such as increasing the heat sink or using advanced cooling systems, can reduce the oil temperature, maintain the performance of the lubricant, reduce the strength reduction caused by friction and overheatingIn summary, by choosing suitable materials, optimizing the structural design, improving the durability and strength of gears, improving the manufacturing and installation precision and strengthening the lubrication and heat dissipation and other measures, the strength of the gear box can be effectively improved to ensure its long-term stable operation.
How to improve the EMI performance
1. Optimized for commutators:
The commutator of a brushed DC motor is one of the main sources of electromagnetic interference. Optimize the contact surface between the commutator and the brush, adjust the carbon crystal composition ratio (hardness), use a suitable varistor, and reduce spark discharge, thereby reducing electromagnetic interference.
2. Use EMI Filters:
Applying EMI filters on motors can effectively filter out the electromagnetic interference generated by the motors. EMI filters are effective in high-frequency filtering, with a wide filtering frequency band and low solution cost.When selecting an EMI filter:
Consider the rated voltage: The rated voltage of the filter must be greater than or equal to the maximum input line voltage provided to the device, and generally 30%-50% higher than the input voltage to ensure that the filter will not be damaged under normal operating voltage.Consider rated current: The rated current of the selected filter should be equal to or higher than the maximum steady-state input current consumed by the device when powered on, to avoid filter failure due to excessive rated current for a long time.
Consider insertion loss: Insertion loss is the ratio of the power received by the load before and after the filter is connected, and the unit is decibel (dB). When selecting a filter, you should choose a filter with a smaller insertion loss to ensure its attenuation effect on electromagnetic interference.
3. Use shielding materials
Use shielding materials such as electromagnetic shielding covers, metal shells or shielding sleeves inside the motor to reduce the propagation and leakage of electromagnetic fields.4. Reasonable design of ground wire
Ensure that the motor ground wire layout is reasonable, use low-impedance ground wire and good grounding to provide an effective drainage path for electromagnetic interference.5. Optimized motor structure
Redesign the motor structure, such as adding insulation and improving the wire layout, to reduce the generation and leakage of electromagnetic interference.6. Adoption of filtering circuits
Add filtering circuits such as capacitors, inductors or LRC filters to the motor input and output lines to suppress the propagation of high-frequency noise and electromagnetic interference signals.
Stranded, EMI-shielded power cord to reduce input electromagnetic interference signals7. secondary filter:
Based on the primary filtering, secondary filtering is performed for the remaining high frequency problems to improve the filtering effect. Be careful to avoid repeating the same type of LC device.
8. Note the effect of the PWM signal
DC brushed motors are often controlled by PWM signals. When filtering, it is necessary to ensure that the PWM signal is not inadvertently filtered out, otherwise the normal operation of the motor may be affected.9. Combined application of multiple measures:
Since the radiation problem of motors involves the entire frequency band, no single device can cover all the frequency bands. Therefore, it is necessary to apply a combination of measures for targeted rectification based on test data.Through the combined application of the above measures, the EMI performance of DC brushed motors can be effectively improved to reduce the impact of electromagnetic interference on the surrounding circuits and equipment. In practice, it may be necessary to adjust and optimize these measures according to specific conditions.
Our Company Advantage
Applications
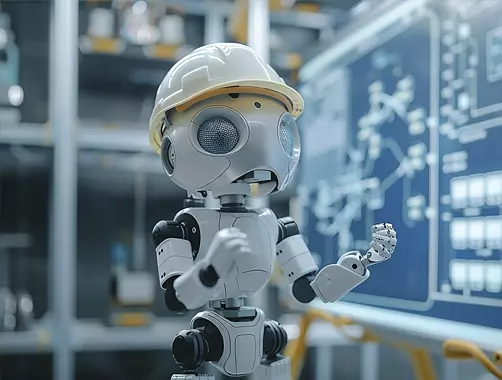
Robotics
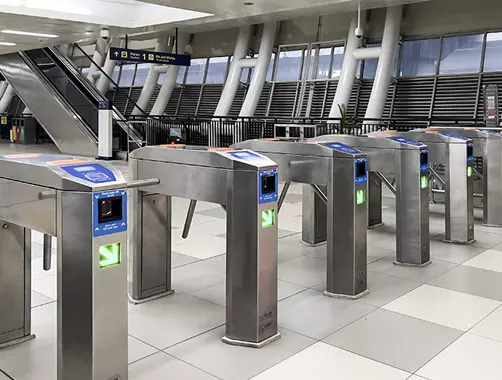
Security
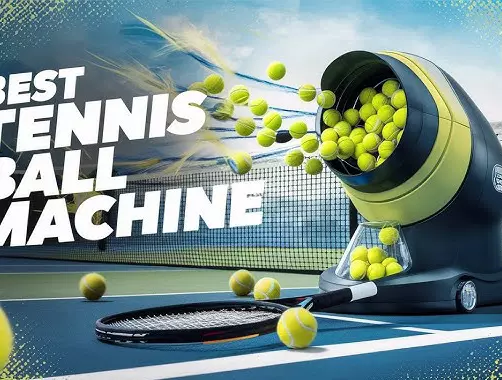
Intelligent Sports Aid Products
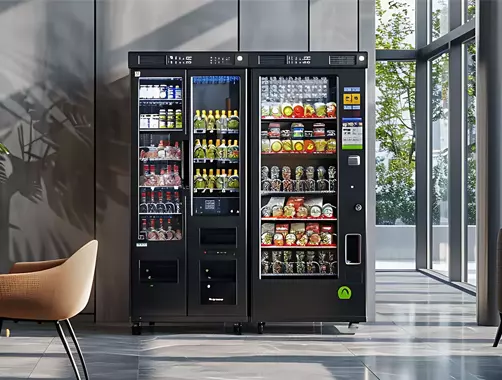
Industrial Products
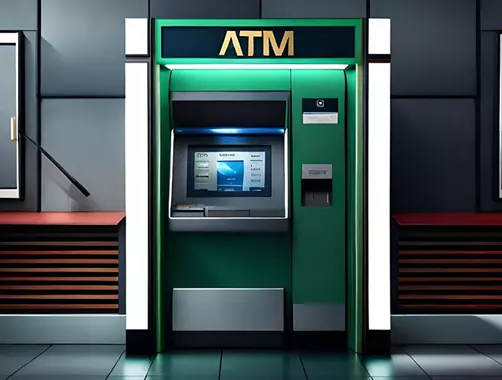
Bank System
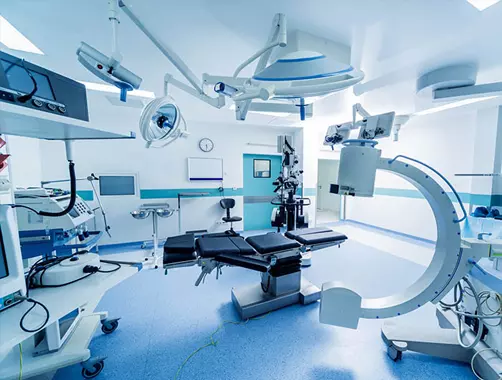
Medical & Health Care
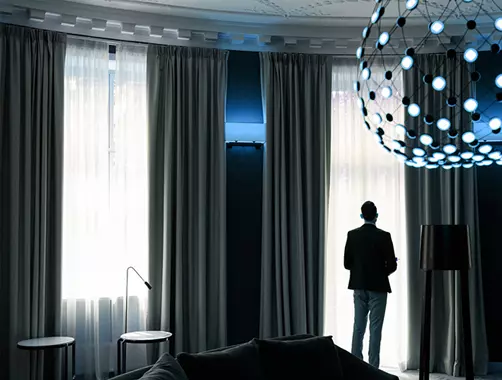
Smart Home
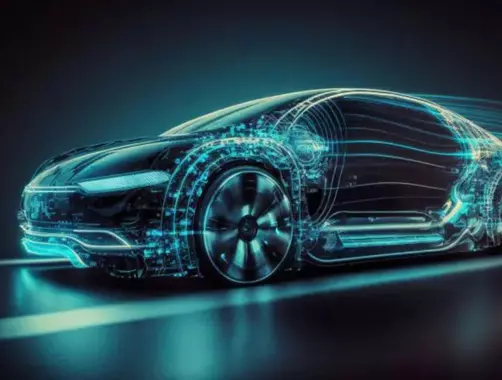